Automation Challenges, Opportunities, and Planning Ahead
Since the start of automation, the workforce has had to transform and shift, adapting and upgrading their skills over time. And despite fears dating back one hundred years, automation has been responsible for creating one-third of all new jobs since then.
Automating Challenges and Opportunities
Robotic automation has been a challenge as well as an opportunity since its very beginning, with humans worrying about losing their jobs to robots since the 1930s. While this trend has never abated, and some economists still believe that automation will lead to more job losses than creation by 2030, additional studies have determined that automation’s impact will be overall positive.
Since the start of automation, the workforce has had to transform and shift, adapting and upgrading their skills over time. And despite fears dating back one hundred years, automation has been responsible for creating one-third of all new jobs since then.
The manufacturing sector particularly could gain from automation, as it could contribute $4.9 trillion to the industry annually by 2030, and save 749 billion working hours by automating 64% of manufacturing tasks.
Employers' and Employees' Perception
On the employer side, 24% have a reduction in operating costs as their main reason for automating their business. According to 57% of employers who are aiming to automate, the goal is to improve the productivity of the workforce.
Overall, automation is seen, more and more, as a positive, albeit scary, change. The World Economic Forum estimates that by 2022, 42% of tasks in manufacturing will be automated, shifting the focus towards more sophisticated, high-value roles and 55% of jobs that do not require college degrees will likely end up being automated.
The economic and efficiency benefits that this could bring to the manufacturing sector cannot be understated. Machines could handle a majority of tasks currently performed by humans, which could—and may—lead to changes in the workforce structure: we would be looking at shifts in skills training, job displacements, but also opportunities for more complex and less monotonous jobs for human workers, a belief supported by the majority of employees. Indeed, 86% of them believe that automation will help them do their work more efficiently, and only 11% see automation as a substitute for human labor. Surveys have shown a strong belief among workers (7 out of 10) that automation will create better opportunities for them in higher-skilled jobs.
Planning for Automation
However, this will only succeed if organizations focus on protecting their employees by helping them upskill, rather than preserving existing jobs. To weather this disruption, women (and men) will need to be skilled, mobile, and tech-savvy. But women face more barriers, and will therefore need more support to move forward. Indeed, between 40 million and 160 million women globally might need to transition between occupations by 2030, often into higher-skilled roles.
As change is happening now—and is accelerating, it’s paramount for companies to plan. We cannot refute that automation is going to affect every level of business, no matter how reticent or enthusiastic people are about this change. As such, companies must turn to their systems and plan accordingly, as they have a responsibility to their people in nurturing, adapting, and re-skilling their employees.
While the majority of workers aren’t currently worried about their jobs, it still leaves one-third who are anxious about the outcome of this major change, and who will need support, encouragement, and motivation to re-skill themselves.
What about AI?
The unlocking of AI, especially when it comes to ChatGPT last year and its subsequent unleashing over all industries, cannot be forgotten. In the manufacturing industry, AI has started to take on a bigger place and is bringing with it problems and opportunities. Linking AI to automation can allow for better accuracy and efficiency, it can reduce processes and lower costs, improving productivity across the board. It is, for all intents and purposes, a wonderful tool for positive change.
But, like with every new big change, this will also lead to job displacements, especially when it comes to jobs that are considered low-skill, high-repetition jobs. Displacement is a good word though, as it implies the rise of new positions as well.
Jobs are not canceled, they are evolving, allowing for new work opportunities rather than their reduction.
As routine, manual tasks become automated, the demand for cognitive and problem-solving skills is expected to rise—soft skills that machines cannot easily replicate. With automation, entirely new job categories are likely to emerge, like the maintenance, programming, and oversight of automated systems.
Soft-skilled employee roles are starting to emerge, with the need for problem-solving and emotional intelligence. Employees will need to learn to adapt, propelled by the support of their companies through training courses, seminars, etc.
England’s example
In England, automation replaced 850,000 workers between 2001 and 2017, but it also created 3.6 million opportunities for new higher-skilled ones.
This is a great example of how in the future, businesses will be able to offer their workers new job opportunities—should they also allow them to grow and advance in their skills.
This progression is not a binary system of humans versus robots: technology can nuance and automate some manual tasks, but it is the company’s mission to ensure that automation benefits everyone in the ecosystem.
As the nature of jobs changes, there will be a significant need for upskilling and reskilling, and companies will play a crucial role in this transition. Supportive policies and frameworks will need to be put in place, such as transition policies and mechanisms for easing the integration of displaced workers into new roles.
If companies can plan for all of their employees, advancements in automation can truly continue to empower—rather than displace—the workforce.
Last news & events about inbolt
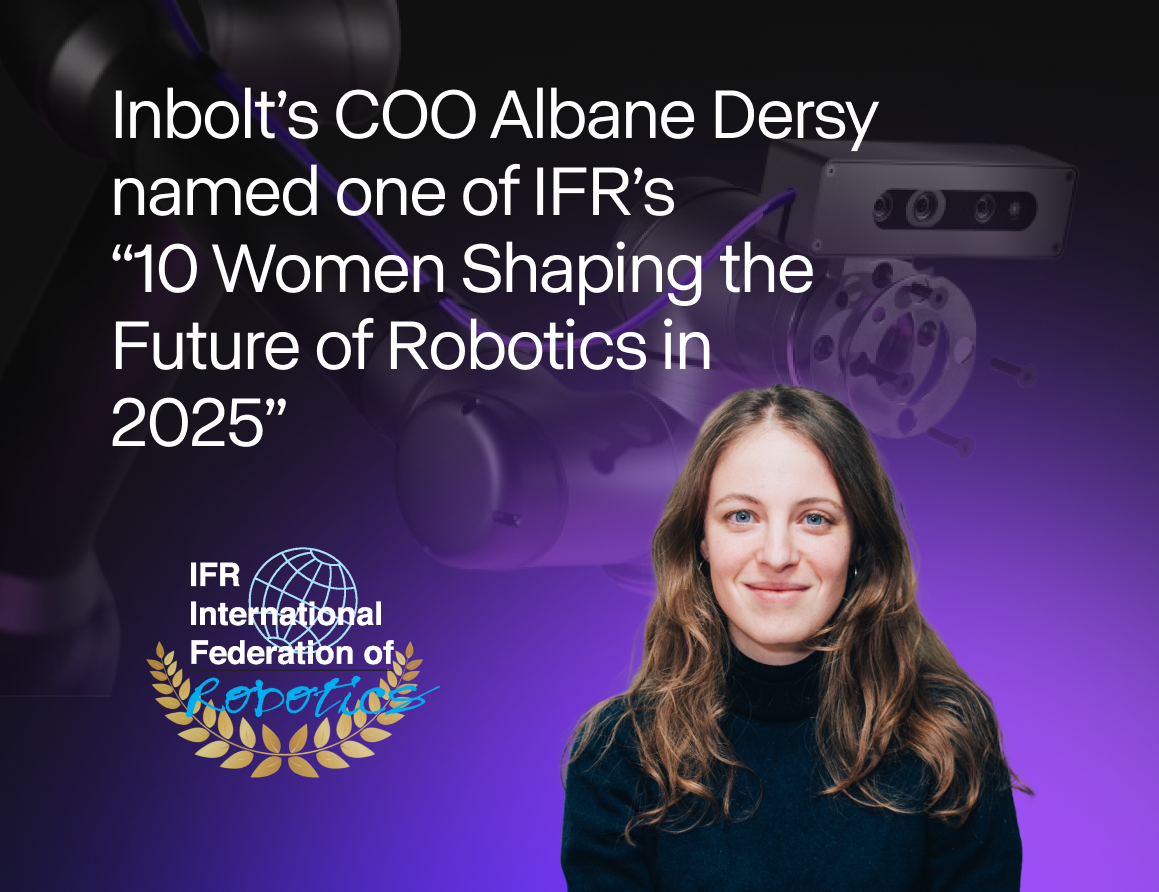
Articles
Albane Dersy named one of “10 women shaping the future of robotics in 2025”
The International Federation of Robotics has recognized Albane Dersy, co-founder and COO of Inbolt, as one of the “10 Women Shaping the Future of Robotics 2025.” At a time when manufacturers are racing to automate, Albane’s leadership stands out for bringing flexibility and intelligence to robotics on a global scale. This article explores her career, the impact of her work with Inbolt, and the leadership lessons she shares with the next generation of innovators.
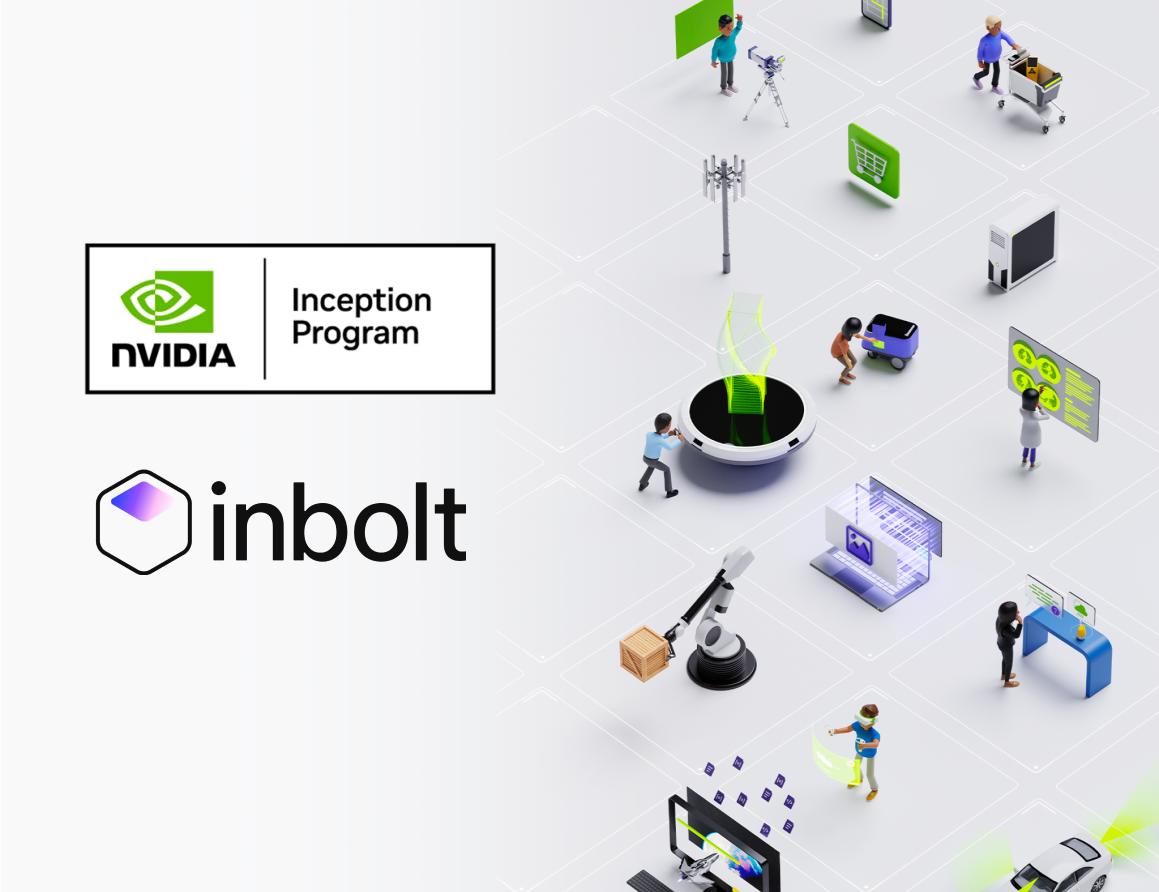
Articles
Inbolt Joins NVIDIA Inception to Accelerate AI-Driven Automation
Inbolt joins the NVIDIA Inception program to boost its AI-driven automation solutions. This partnership provides access to exclusive resources, accelerating Inbolt’s mission to enhance real-time 3D vision for robots in manufacturing.