Dynamic and Fixed/Static Environment in the Automation Industry
Looking to automate your manufacturing process? Learn about the differences between dynamic and fixed environments and how they impact productivity and cost savings. With the right approach, shifting to a dynamic environment can result in tremendous gains in efficiency. At inbolt, our GuideNOW system provides flexibility in production and enables real-time decision-making for industrial robots.
Dynamic environment
A dynamic environment refers to a workspace or manufacturing process in which workpieces are continuously moving and workers and robots are required to perform operations in real-time. This type of environment is commonly found in industries such as automotive, electronics, food and beverage manufacturing, where high productivity and efficiency are crucial.
The concept of a dynamic environment can be traced back to the development of the continuous moving line by Henry Ford in the early 1900s. Today, continuously moving lines are commonly used in a variety of industries to increase productivity and reduce costs. It’s a tried and true process that, generally speaking, works.
However, working in a dynamic environment can be challenging for robots. Indeed, robots, by design, will have a mission and a goal, and may have difficulty adapting to the unpredictable movements of a moving workpiece. This can lead to unplanned events such as abrupt stops, vibrations, and shifts in position, which can be difficult for robots to handle without proper sensors and programming. These types of events aren’t as confusing for humans, who can generally make adjustments in real-time.
We’ll remember that it can be challenging for robots to adapt to unpredictable movements in dynamic environment.
Fixed/Static environment
A fixed/static environment refers to a workspace or manufacturing process where a workpiece remains stationary at a fixed workstation while workers or robots perform operations on it. This type of environment is commonly found in industries with longer cycle times, such as aerospace and heavy equipment manufacturing, where the workpieces are typically large and require multiple operations.
While a fixed environment may result in a loss of productivity compared to a continuously moving line, it can be easier to automate and control the positioning of the workpiece. Since the workpiece is fixed in one location, it is possible to constrain and index its position, making it easier for robots to perform precise and repeatable operations. This can result in lower costs and increased efficiency over manual labor, especially in these specific industries.
Read our article about Structured and Unstructured environments here.
Shifting the manufacturing process from a fixed environment to an automated, dynamic environment can result in tremendous gains in productivity and cost savings. By eliminating the time lost between workstations on a moving line, manufacturers can significantly increase their throughput and achieve their production targets more efficiently.
We’ll remember that a fixed environment can be easier to automate and control, but isn’t as flexible and harder, if not impossible, to reprogram.
Case study
At inbolt, we computed that for a classic automotive manufacturer, shifting the manufacturing of electrical engines on a moving line could represent CAPEX savings of up to 29.98% to reach their production target. By improving the productivity and flexibility of just one line, there wouldn’t be as much of a need to build another line. In this case, the manufacturer could manufacture as much as 500 000 engines/year with only 3 lines instead of 4.
Learn more about how much you could save, reach out!
Limitations
Automating a dynamic environment can be quite complex, as it requires an array of sensors and systems, as well as an effective cell deployment.
The implementation of a dynamic environment for manufacturing electrical engines would require a range of technologies: encoder systems, mechanical robot indexing systems, and vision systems. These technologies can be expensive and complex for the end-user to use effectively.
Overall, whether a dynamic or fixed environment is more suitable for a particular manufacturing process depends on a variety of factors (type of workpiece, required cycle time, desired level of automation). But despite the challenges, the gains of automating a dynamic environment can be tremendous, and are certainly an avenue worth exploring.
The inbolt Advantage
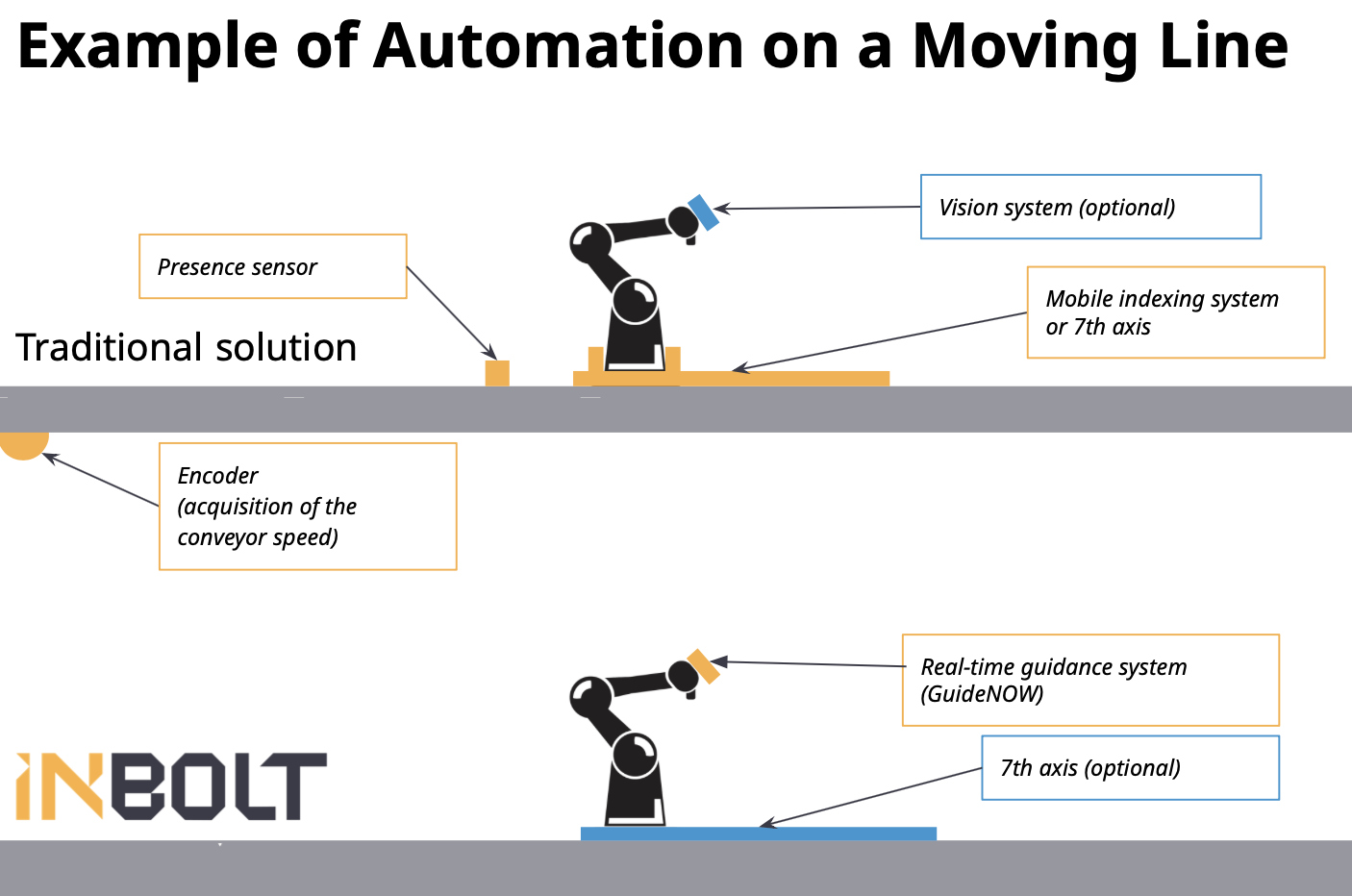
One advantage of using our GuideNOW system is the flexibility it provides in production. Indeed, our mission is to create a vision layer for industrial robots that enables real-time decision-making and ensures their successful integration into any type of environment, from fixed to flexible. We use advanced technology to track the workpiece position by comparing the CAD model with 3D data from the camera, and performing computations at a very high frequency that almost parallels real-time. This approach makes it easy to automate moving lines, as our solution replaces multiple systems such as encoders, line trackers, and vision systems.
On a fixed station, inbolt’s solution will decrease the need for jigs and indexation, making it ideal for high-mix, low-volume (HMLV) production. The solution works thanks to a CAD Model, or a scan, of the workpiece. It makes the solution easy to set up. No need to constrain the environment or to use markers. This is useful, especially for customers with a high mix of products manufactured.
On a moving line, inbolt’s solution offers increased flexibility and allows the mission to be completed while the system is in motion.
This feature is becoming essential, saving valuable time during production and boosting efficiency. Additionally, the GuideNOW system’s flexibility allows the production line to be re-organized or adapted faster and at a fraction of the cost compared to fixed lines.
If you’re wondering whether your automation needs fit inbolt’s mission, reach out!
Last news & events about inbolt
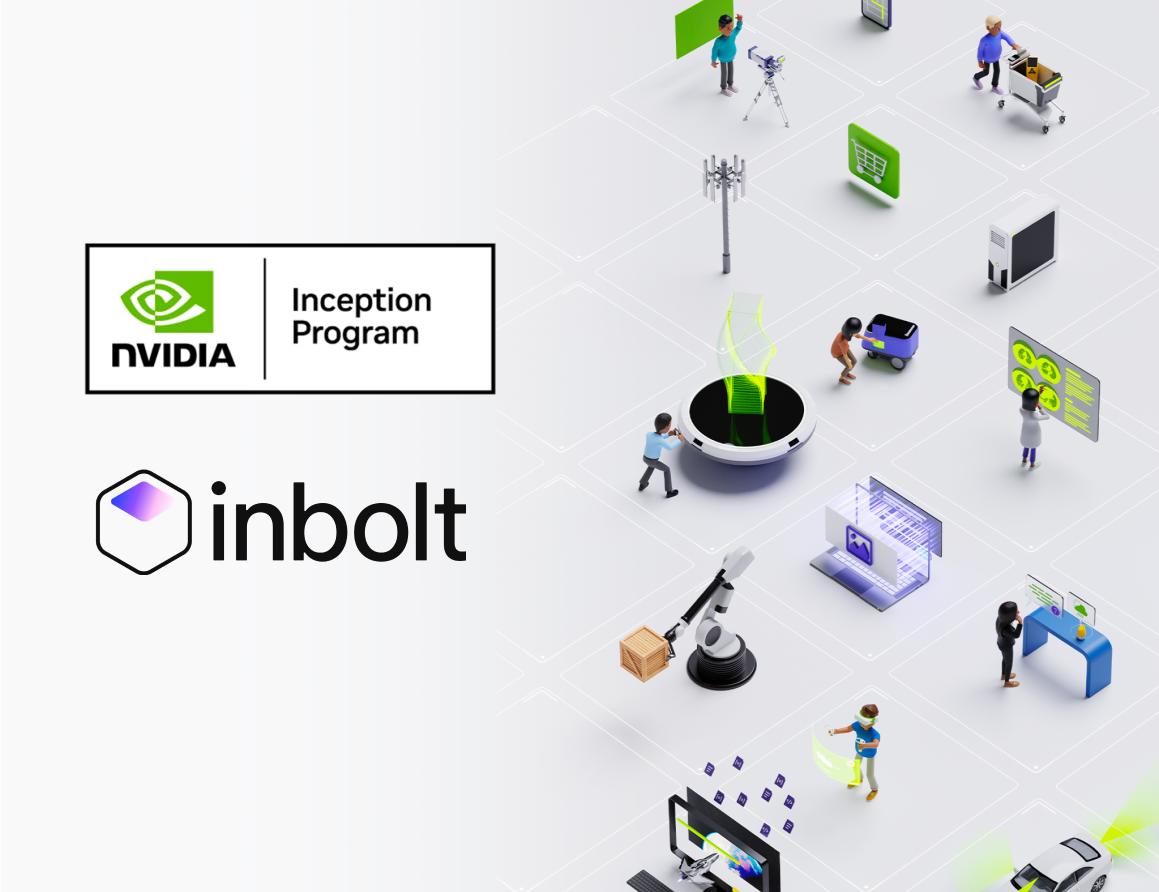
Articles
Inbolt Joins NVIDIA Inception to Accelerate AI-Driven Automation
Inbolt joins the NVIDIA Inception program to boost its AI-driven automation solutions. This partnership provides access to exclusive resources, accelerating Inbolt’s mission to enhance real-time 3D vision for robots in manufacturing.